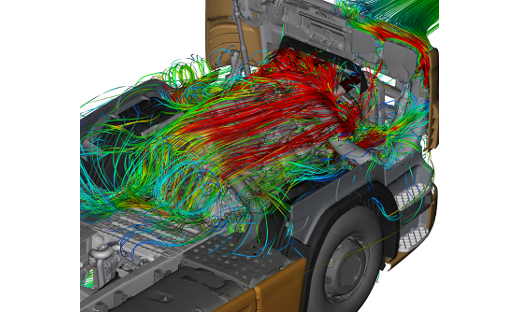
Investigate the function and potential of cooling air ducts through CFD-simulations and give design suggestions on how such cooling air ducts should be designed to give desired results; notably lower the engine compartment temperatures at the rear end of the engine.
Description of Work
The high temperatures in the engine compartment arise when cooling air from the engine cooler and fan (~100 ºC) is heated by warm components such as the exhaust manifold and turbo. Behind the engine and the driver cabin the hot air is diluted when it is spread with the surrounding air and larger air volumes.
One way to lower the temperature load on the components at the rear end of the engine is to guide outside air through a front or side duct installation. The outside air (~25 ºC) cools down the hot engine compartment air as it travels backwards in the truck. The difficulty is that there is a local high pressure zone in the engine compartment and a low pressure zone on the outside of the truck.
The air duct should preferably be designed to self ventilate since, for example, electrical fans imply a complex installation and costly electrical consumption. The location of the air ducts needs to be adapted to the existing pressure distribution that is built up around the vehicle during travel to achieve self ventilation.
The air duct will be designed and tuned with the CFD software Star-CCM+. If the work leads to successful designs there is a possibility to make physical testing in wind tunnel.
Prerequisites
M.Sc./Master program final year students with background in fluid dynamics and a keen interest in fluid dynamics and CFD-simulations.
Number of Students
Suitable for one or preferably two students, for example, one analyzing an extra front air intake and the other student a side air intake.
Start Date (suggested)
January 28th 2013.
Estimated Time Needed
20 weeks during spring 2013.
Contact
Supervisor Mattias Chevalier (CFD), 08-553 53097, mattias.chevalier@scania.com.
Manager Per Jonsson (CFD), 08-553 85272, per.jonsson@scania.com.
The work will be co-supervised by Dan Henningson at the Department of Mechanics, KTH.
Application to
Label the application “FU12-83” and send it to erica.flodin@scania.com.
Enclose CV, personal letter and school grades.
Application Deadline
November 30th 2012.